The new manufacturing lab at the University of North Texas could put Denton’s engineering school at the forefront of 3D printing technology. In the lab, engineers are working to change the way many things are made.
Inside a sealed, clear box filled with argon gas, one of UNT’s 3D machines is busy printing away, accompanied by its own humming, buzzing soundtrack.
“For this particular thing we are making is actually a soft, magnetic alloy,” says UNT engineering Professor Raj Banerjee, who helped launch this new lab in November.
“Because,” Banerjee adds, “there’s a lot of potential of 3D printing for next generation magnetic components. And so we are working on some magnetic alloys based on a combination of nickel and iron.”
Banerjee says this 3D printing process is also known as additive manufacturing. The printer adds material one thin layer at a time. Plastic pellets or metal powders are placed on a platform, heated with a laser before another layer goes on top of another and another until it’s done.

For 28 year-old graduate Saket Thapliyal, 3D printing is the future.
“Some materials are good at bending,” Thapliyal says. “Other materials are good in tension. So we can use graded structure in a same product. To my knowledge it’s not done yet.”
But this lab is working to get it done. 3D printing has been around three decades even though to many it seems new. And while 3D objects look nice, there’s been a long-standing problem. They often fail — in medicine or aerospace — because they’re not durable. For example, Banerjee says 3D printed parts for high stakes jet engines have for years broken down. This lab’s working to solve that by creating completely new materials.
“We want to focus on what is happening to these metals and alloys,” Banerjee says, “as well as the futuristic materials, like ceramics as well as metal-ceramic composites, which have not even been matured for additive manufacturing, but we want to explore those domains.”
Because, says UNT Research Professor Narendra Dahotre, who helped engineer this 3D lab, that will truly expand the horizons of additive manufacturing.
“It will let us do things which were never possible to be done in the past,” Dahotre says.
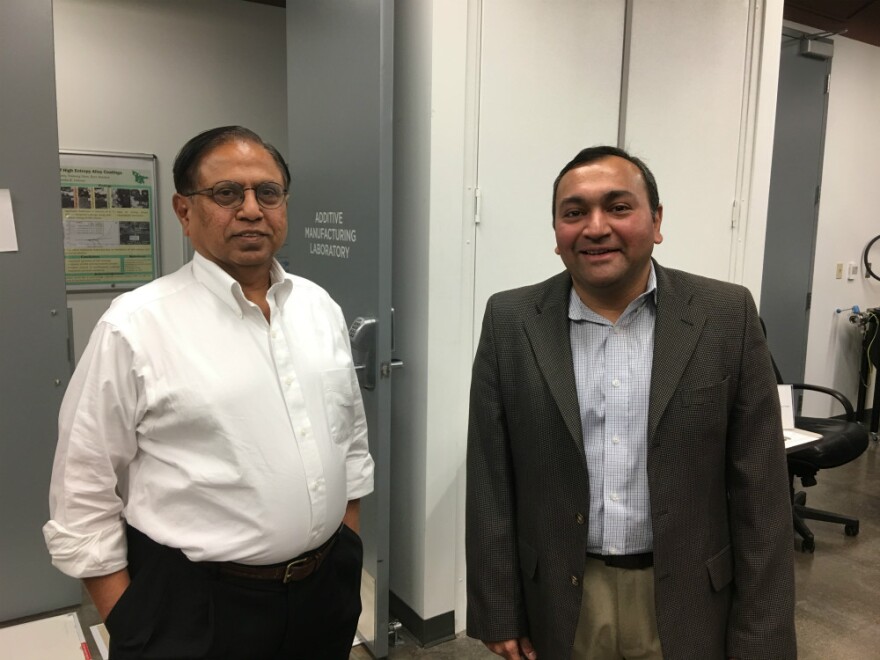
Things like creating the next generation of surgical pins and plates, which are currently made of titanium. Orthopedic surgeon Dane Wukich says that helps and hinders.
“If you have a fracture and you put a plate in — a piece of metal — it provides an internal splint right away so your bone has support and you’re not flopping all over the place,” Wukich says.
It's great for the broken bone, says Wukich, chair of orthopedic surgery at UT Southwestern Medical Center. But it's not great for the healthy bone on either side of the break. That bone needs stress to stay healthy. But Wukich says the stiff, titanium implant weakens it by taking on all that stress.
“The bone adjacent to the plate undergoes atrophy,” Wukich says, “and becomes almost like osteoporosis, and that is subjected to what we call a pathologic fracture.”
Doctor Alan Jones, chief of orthopedics at Baylor University Medical Center, imagines a solution that doesn’t yet exist.
“One thing would be to have a strongest part of the plate in the middle and then gradually become more flexible and stuff as you get to the end,” says Dr. Jones.

That’s not possible with titanium alone. Banerjee says UNT’s lab has 3D-printed a new type of surgical plate material. Holding it in his hand, he says it contains surgical titanium in one section, but also niobium in another, and zirconium.
“As you can see it’s a single block of metal,” Banerjee says, a smile breaking across this face. “I can make this only using 3D printing technology today. And now you can’t even see the layers. But it actually has a variation in the stiffness so it is very stiff in the center and much more compliant at the edges.”
This 3D plate is still years from use and must prove safe and effective. But it may be just what the doctor ordered.